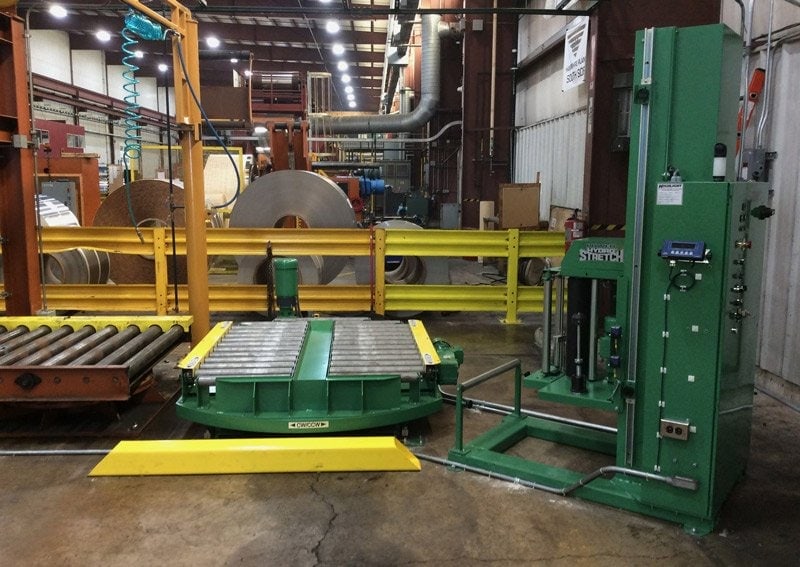
Executive Summary
Best Packaging was able to deliver a fully customized packaging solution incorporated directly into the client’s production line. The result was more efficient use of time and floor space while minimizing safety risks in their procedure.
Customer Background
Elgiloy Specialty Metals, based in Elgin, Illinois manufactures high performance metal alloys. In their Hampshire, Illinois facility, they produce large industrial coils, which must be strapped and stretch wrapped in order to prepare for shipping.
Challenges
Prior to Best Packaging’s involvement, Elgiloy’s coils had to be removed from the conveyor line and driven by forklift to a nearby semi-automatic stretch wrapper. From there, laborers would attach the stretch film, operate the machine to wrap in an upward spiral, pause to apply a top sheet to the coil, then allow the machine to complete its process in a downward rotation. In all, this process was inefficient as the production line must be paused to remove the coils. Production speed was limited to the fork lift operator’s capabilities.
Solution
Elgiloy aimed to incorporate a fully automatic, stretch wrapping solution directly into their conveyor line, which would eliminate the need to stop the conveyor while removing the coil.
Best Packaging customized a solution that took a three-pronged approach to increase efficiency.
The new line design incorporated a heavy duty, fully-automatic stretch wrapper capable of rotating pallets up to 8000 lbs, or four tons.
A scale was incorporated into this machine to record pallet weight.
The new end-of-line system incorporated specialized strapping channels that would allow each coil to be strapped to a pallet while on the conveyor, prior to being wrapped. This provides greater containment force than strapping post-wrap.
In addition to embedding this three-in-one machine directly into Elgiloy’s end-of-line, Best Packaging made a series of conveyor upgrades including a switch from liquid-type conduit to rigid conduit. Best Packaging added the ability to manually control the powered conveyor using a push-button and toggle-switch remote station. This enabled the customer to manipulate their product’s positioning on the conveyor prior to palletization in order to ensure the best fit.
In effect, the product is loading-dock ready before it rolls off the conveyor.
The Results
For over a year, a team of line technicians from both parties worked together to fine-tune this custom solution. By May of 2020, the new design was fully incorporated at the Hampshire, lllinois facility. Throughout 2020, Best Packaging continued to provide programming support to meet Elgiloy’s specifications.
Since then, Elgiloy has reaped the benefits of a fully incorporated solution through eliminating bottlenecks for increased efficiency while minimizing the safety risks associated with moving extremely large and cumbersome materials.
FUTURE APPLICATION
Best packaging offers objective evaluations and ROI analysis, innovative designs and technologies that improve performance. Our technicians are experienced in integrated line design and are able to create effective conveyorized systems, custom-tailored to your facility’s needs. Request an audit today by contacting info@bestpackaging.com, or call 888-930-best!