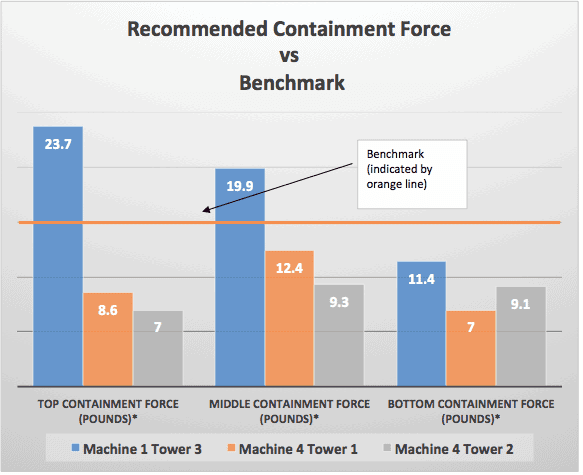
Executive Summary
The Customer that reached out is a leader in marketing and distributing food and food-related products to restaurants, and healthcare and educational facilities. They requested our film audit service for their facility to determine current and 1-year projection consumption. Corporate requires all facilities to purchase stretch film from approved vendors, which raises concerns about the quality of stretch film the Customer receives.
Customer Background
Elgiloy Specialty Metals, based in Elgin, Illinois manufactures high performance metal alloys. In their Hampshire, Illinois facility, they produce large industrial coils, which must be strapped and stretch wrapped in order to prepare for shipping.
Observations
Using our Computerized Load Cell System, we discovered different levels of containment force are being deposited on the top, middle, and bottom of the load.
We detected the same model of film was varying roll-to-roll depending upon what production line it ran on. We found that the same model stretch wrapping machinery oftentimes performed differently. We also noticed that operators were making subtle changes to the equipment for a variety of reasons: customer complaints, film breakage or what they thought would run better.
Solution
Rather than standardizing film we found that we had more success when we standardized the result. We managed to achieve the same results regardless of where the film was purchased. We made the proper adjustments needed to ensure that loads met the benchmark of 11.5 lbs. of containment force throughout the top, middle and bottom of the load. Best Packaging Technicians trained the Operator on how to make sure the machine is running at it optimal condition to maintain the standard.
Goal
Share information that will help the Customer develop a best practices strategy to get the most value and production from their stretch film purchases while insuring that their products arrive damage free.
Analysis
We reviewed the properties of the film to determine the best stretch level or “Sweet Spot. Once we determined the benchmark, we observed that most of the results were significantly below what is recommended.
Our research indicated that if the company continued using the same settings, the approx. rolls of film consumed in 2019 would be 6,900 and the approx. spending would be $450 based on 1,600 pallets per shift. However, proper benchmarking, machine set up and film type can reduce this number of rolls consumer to 2,824 and the spending to $180,000
WANT MORE INFORMATION?
For a more in-depth data and analysis of this particular case study, click the button below