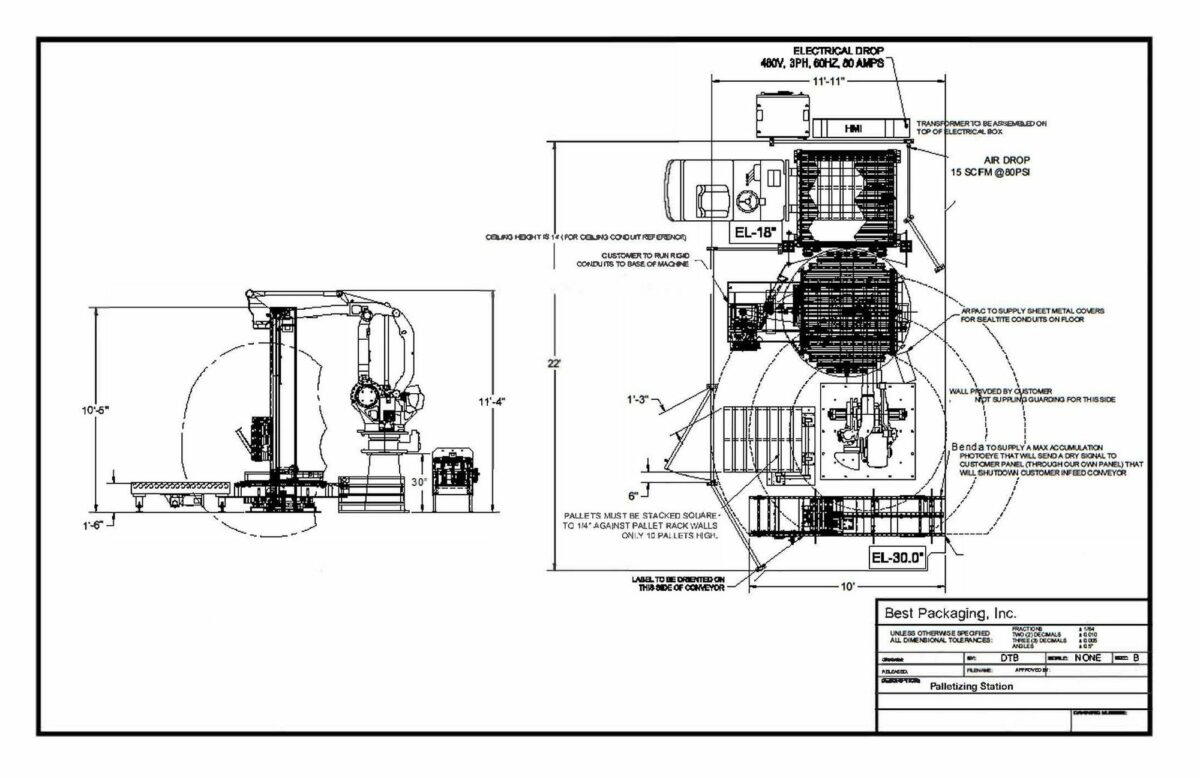
Customer Background
The customer was a large meat manufacturer supplying meat to national restaurant chains and food manufacturers who use their protein to deliver refrigerated and frozen meals found in grocery stores across the United States.
Problem
A protein manufacturer was growing at an exponential rate. The facility was due for an expansion, but due to space constraints, the customer had been using manual labor to palletize and wrap cartons. The customer sought Best Packaging’s help for recommendations on small pieces of equipment.
Solution
A fully-automatic small footprint palletizing and wrapping cell was designed to automate the process. Other than needing an operator to deliver stacked pallets to a holding area, the process was fully automatic. The cell programming was designed to accommodate automatic changeovers of pallet packs to meet customer specifications. Best Packaging’s solution offered the following:
- Reduction of labor costs & damage
- Rise in productivity
- Reduction of worker comp claims
- Higher quality packing
Observations
- 40 cartons was too heavy for an operator to handle effectively.
- The loads were up to 90” tall requiring the use of a stand to palletize.
- The pallet pack changeover was often missed and the speeds of up to 10cpm were too fast for an operator to handle.
- The space was not big enough to accommodate large equipment.
Results
The new efficient process had a payback of less than 24 months.
GET STARTED
Best Packaging offers objective evaluations and ROI analysis, innovative designs and technologies that improve performance. Find out today how Best Packaging can provide the best solution to address your business needs.